Understanding Six Sigma: Principles and Applications
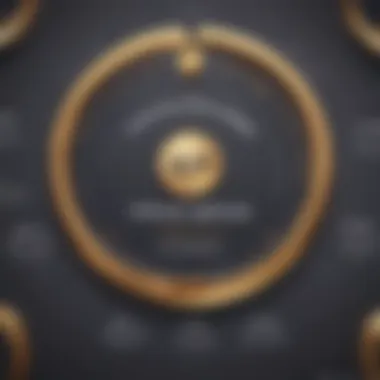

Intro
In the fast-paced world of business, the need for effective methodologies that streamline processes and eliminate waste is paramount. One of the most recognized frameworks that fulfills this need is Six Sigma. But what exactly does Six Sigma entail? How did it come about, and what are its implications for organizations today?
At its core, Six Sigma is a data-driven approach to eliminating defects and improving quality in any process. Its principles are applied across various industries, from manufacturing to healthcare, showcasing its versatility.
Through this article, readers will embark on a comprehensive exploration of Six Sigma. From its historical roots to its practical applications, we will provide insights aimed not just at experts, but also at newcomers who may be sipping the tea of modern business methodologies for the first time.
Crucially, it's essential to grasp the terminology and framework that shape Six Sigma practices. Terms like 'defects', 'process variations', and the roles of 'Belts'—Yellow, Green, and Black—are foundational to understanding this methodology's mechanics. This article will equip readers with the knowledge and tools needed to apply Six Sigma principles effectively, opening doors to enhanced operational efficiencies.
Ultimately, this deep dive into Six Sigma aims to empower investors, finance professionals, educators, and students alike. By grasping how Six Sigma functions and its potential impact on their respective fields, they'll have the key to unlocking greater productivity and quality.
Investment Understanding
Six Sigma's framework enables a fundamental understanding that is quite similar to investing—it's an initiative that requires knowledge, patience, and a methodical approach.
Key Terms Explained
Before diving deeper, let's clarify some essential terms surrounding Six Sigma:
- Defect: Any instance where a process fails to meet customer satisfaction.
- Standard Deviation: This measures how data points disperse from the average in a given process.
- DMAIC: An acronym representing the core methodology for existing processes—Define, Measure, Analyze, Improve, and Control.
- Belts: These indicate levels of expertise within Six Sigma, ranging from Yellow Belts, who have basic knowledge, to Black Belts, who lead strategic projects.
Understanding these terms is crucial in navigating through the intricacies of Six Sigma’s concepts and practices effectively.
Types of Investments
Similar to how investors diversify their portfolios, organizations can also employ a variety of Six Sigma tools and techniques. Each type serves a unique purpose in enhancing processes and ensuring performance optimization. Here’s a brief overview:
- Root Cause Analysis: Used to identify the underlying factors causing defects.
- Process Mapping: Helps visualize steps in a process to find inefficiencies.
- Statistical Analysis: Employed to measure performance and identify areas for improvement.
By aligning these tools with project goals, businesses can see tangible returns on their investment designed to yield continuous improvement.
Fundamentals of Six Sigma
Six Sigma stands as a cornerstone for organizations striving for excellence. It's not merely a set of techniques; it is a comprehensive philosophy that emphasizes quality, efficiency, and continuous improvement. By understanding its fundamentals, businesses can significantly reduce defects, elevate customer satisfaction, and consequently enhance profitability.
Definition of Six Sigma
At its core, Six Sigma is a data-driven methodology aimed at reducing variation in processes to improve overall quality. The term "Six Sigma" itself relates to the statistical term that symbolizes only 3.4 defects per million opportunities. This level of quality serves as the benchmark for organizations that wish to minimize errors and maximize efficiency. In other words, if a company achieves Six Sigma performance, it’s effectively operating at near perfection, which leads to a competitive edge in today’s market.
Historical Context
Origins in Manufacturing
The roots of Six Sigma stem from the manufacturing industry, particularly during the 1980s when businesses faced unprecedented pressure to improve quality while lowering costs. Motorola was one of the pioneers, implementing Six Sigma as a way to tackle the growing problem of defects and inefficiencies in production lines. The key characteristic here lies in the methodology's initial focus on rigorous statistical analysis to fine-tune manufacturing processes. This approach ensured that every step, from raw materials to final products, met stringent quality standards.
In essence, the practical application of Six Sigma in manufacturing provided a structured framework for problem-solving. The unique feature of this origins story is its adaptability; what began as a manufacturing tool has evolved to cater to various sectors, showcasing its versatility. However, the approach can be resource-intensive, requiring a deep understanding of statistics and a commitment from management to foster a culture of quality.
Evolution into Service Industries
As businesses began to recognize the limitations of viewing Six Sigma solely through a manufacturing lens, the methodology evolved into the service sectors. The key shift involved applying the same rigor and data-driven principles to processes like customer service, healthcare, and finance. This evolution demonstrates Six Sigma's value beyond just products but also emphasizes the quality of service delivery.
For instance, in hospitals, Six Sigma has been employed to streamline patient care processes, minimize medication errors, and optimize scheduling systems. Its adaptability is a major benefit, allowing organizations in various fields to make substantial improvements in their operational capabilities. However, this transition often comes with challenges; service industries might experience resistance to change as they navigate the complexities of shifting organizational culture.
Implementing Six Sigma effectively requires not just tools, but a comprehensive change in mindset throughout the organization.
The distinction of utilizing Six Sigma techniques in service environments underscores the potential for widespread applicability. Although different, the principles remain rooted in the focus on process improvement, emphasizing measurable results that can drive success in any sector.
Objectives of Six Sigma
The objectives of Six Sigma serve as the compass that guides organizations toward operational excellence. Understanding these objectives is crucial for anyone involved in process improvement efforts. Notably, the methodology does not merely aim at reducing defects; its scope encompasses a broader range of performance enhancements that lead to increased organizational efficiency and improved customer satisfaction.
Defect Reduction
At the heart of Six Sigma is the clear objective of defect reduction. Defects can be anything from minor errors in a manufacturing process to significant shortcomings in service delivery. The crucial aim here is to minimize these errors, which can have far-reaching consequences on costs and customer satisfaction. An organization that manages to reduce defects stands to gain a competitive edge. For instance, in a car manufacturing plant, even a small oversight can lead to expensive recalls and loss of reputation. To mitigate such risks, Six Sigma leverages statistically-based methods. Through its methodologies, it aims to push processes to operate within a more controlled environment, recognizable by its goal of achieving near perfection, typically measured as only 3.4 defects per million opportunities.
Improving Quality Control
Equally important is the objective of improving quality control. Picture an assembly line producing high-end electronics, where quality is non-negotiable. Six Sigma’s structured approach helps in establishing robust quality control systems. These systems play a significant role in monitoring process variations, ensuring conformity to specifications. In practical terms, Six Sigma equips teams with tools that systematically evaluate processes. For instance, a company providing software solutions might use Six Sigma techniques to regularly test its products, identifying bugs before release. This proactive stance on quality enhances customer trust and reduces long-term operational expenses.
Enhancing Operational Efficiency
Finally, let us consider enhancing operational efficiency. Streamlining processes through Six Sigma leads to significant time and cost savings. For example, a hospital aiming to reduce patient wait times can apply Six Sigma principles to analyze and redesign patient flow. Rather than merely addressing symptoms, this approach examines each step of the process to identify bottlenecks. When operational efficiency is at its best, resources are utilized effectively, waste is minimized, and overall productivity is maximized. As a result, organizations do not just operate faster but can prioritize value-added activities instead of squandering time on rework or redundancies.
In summary, the objectives of Six Sigma are multifaceted, driving organizations to reduce defects, enhance quality control, and improve operational efficiency. Each aspect is interlinked, ultimately fostering a culture of continuous improvement and excellence.
Dedicating resources toward understanding and implementing Six Sigma objectives is not merely a choice; it is an investment in sustainability and growth.
By aligning these objectives with strategic goals, organizations can better navigate the complexities of their industry and continuously evolve to meet customer expectations.
Whether you are an investor assessing a company’s operational health or a student seeking to understand effective management practices, the objectives of Six Sigma offer valuable insights into the way successful organizations operate.
Methodologies of Six Sigma
The methodologies of Six Sigma form the backbone of its successful implementation. They provide structured approaches tailored to address the distinct challenges an organization may face. Each methodology, whether DMAIC or DMADV, serves specific purposes and offers a framework that aids teams in achieving their objectives effectively. Understanding these methodologies is key, as they empower organizations to break down complex processes into manageable parts, enabling better analysis and decision-making.
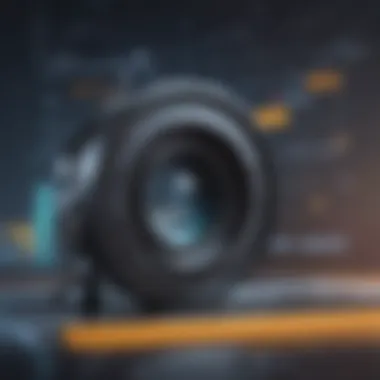

DMAIC Framework
The DMAIC framework stands for Define, Measure, Analyze, Improve, and Control. It's extensively used when the task is to improve an existing process that is not performing up to snuff. The structured progression through its phases not only clarifies objectives but also keeps efforts focused.
Define
The Define phase marks the starting point of the DMAIC framework. During this pivotal step, teams clearly articulate what the problem is. This includes specifying goals and customer requirements, which are vital for subsequent phases. One characteristic that stands out about Define is that it draws attention to the voice of the customer. Understanding what customers expect helps shape project objectives accurately.
The major advantage of this step is its emphasis on clarity. Without a defined problem, it’s like shooting in the dark and hoping for a bullseye. However, if teams don’t invest enough effort in genuinely understanding the problem here, it can lead to misguided efforts down the line.
Measure
Following Define, Measure centers around data collection. It’s here that teams ascertain how the current process is operating through quantitative metrics. The key characteristic of Measure is the reliance on data-driven evidence, allowing organizations to baseline their performance.
This approach is beneficial since it removes guesswork; concrete data provides insights into the nuances of a process. Nevertheless, it’s crucial to note that poor data quality can cloud conclusions, leading to incorrect analyses in later phases.
Analyze
In the Analyze phase, the focus shifts to identifying the root causes of the defects that were pinpointed during the Measure phase. Teams employ various statistical tools to dig deeper. What’s noteworthy about Analyze is its systematic investigation into data patterns. Without thorough analysis, the potential for misunderstanding underlying issues increases substantially.
This phase allows organizations to pinpoint precisely where processes break down, reducing the risk of misallocation of resources. However, if teams rush through this step, they may overlook essential factors that contribute to the challenges at hand.
Improve
Improve is where creativity and strategy blend together. Teams brainstorm potential solutions based on insights from the Analyze phase. The important aspect of this step is that it focuses on generating actionable improvements. Ideas that are selected can have a direct impact on efficiency.
A unique feature of Improve is its emphasis on testing solutions through pilot runs. This trial approach is advantageous as it mitigates risk. Still, implementing changes without adequate planning can lead to further disruptions, so navigating this carefully is a must.
Control
Finally, the Control phase ensures that the improvements made in the previous phase are sustained over time. This phase typically involves setting up monitoring systems. Its key characteristic is a focus on maintaining gains, ensuring that improvements are not merely fleeting.
What sets Control apart is its proactive approach to sustaining progress. With the right tracking metrics in place, organizations can ensure they maintain their hard-won successes. However, neglecting monitoring after improvements can lead to regression, making continuous vigilance necessary.
DMADV Framework
In situations where the aim is to create a new product or process rather than improving an existing one, the DMADV framework comes into play. DMADV stands for Define, Measure, Analyze, Design, and Verify. Organizations benefit from this methodology by ensuring quality from the onset of a project.
Define
Much like the DMAIC framework, the Define phase of DMADV emphasizes the importance of understanding customer requirements and project objectives. It kicks off the project with a clear definition of what the intended outcome should be. This phase is widely regarded as a key characteristic because it lays the groundwork for all subsequent work.
The unique feature here is the comprehensive clarity achieved around project goals, which helps in aligning team efforts from day one. However, if initial objectives are unrealistic, the entire project may be doomed from the start.
Measure
In Measure, teams collect and analyze data regarding product specifications and performance metrics. This step is critical as it shapes the foundation of how the new product is expected to perform. Measure’s key characteristic is its focus on understanding and verifying factors that contribute to quality.
This phase proves beneficial because it equips teams with vital information that guides design choices. However, the challenging aspect can be the complexity of data collection, especially regarding new products where historical data may be scarce.
Analyze
During the Analyze phase, teams sift through the data collected to draw conclusions about design alternatives. The key characteristic of Analyze is its critical focus on evaluating options based on data insights. Teams weigh pros and cons of potential design choices at this stage.
A noteworthy unique feature is the emphasis on predictive analysis, allowing teams to foresee how certain designs might perform. However, relying too heavily on predicted outcomes, instead of empirical data, can lead to decisions that falter.
Design
Design transforms concepts into actionable plans, creating detailed specifications for the process or product. The design step is crucial when it comes to ensuring that customer needs are met effectively. The key point to note is that this phase incorporates feedback mechanisms to refine designs further.
The advantage here is the ability to iterate on designs potentially leading to innovation. Nonetheless, if the design phase is rushed, it may result in a subpar final product or process.
Verify
The last phase, Verify, ensures that the design works as intended before full-scale rollout. It’s all about checking to see if everything aligns with the earlier customer specifications. A key feature of Verify is the thoroughness of quality assurance assessments it undertakes.
This process is immensely beneficial as it mitigates risk by catching potential issues ahead of time. Yet, failure to conduct comprehensive verification may leave teams in the lurch, confronting issues post-launch that could have easily been avoided.
Roles Within Six Sigma
The structure of Six Sigma is not just a set of techniques and tools; it thrives on the people who inhabit its various roles. These roles ensure that the methodology gets implemented effectively and has the desired impact on quality and efficiency within organizations. Understanding these roles, such as the different types of Six Sigma belts and the composition of project teams, enriches any discussion on Six Sigma and adds depth to its application in real-world scenarios.
Six Sigma Belts
In Six Sigma, the concept of belts plays a crucial role in defining expertise and responsibility. Each belt color represents a level of understanding and skills in applying Six Sigma principles.
Yellow Belt
The Yellow Belt is often the entry point for many who start their journey into Six Sigma. These practitioners play a supportive role in projects, mainly focusing on identifying issues and opportunities within processes at a foundational level. They are trained to be aware of Six Sigma principles and can contribute to project teams but typically don't lead projects themselves.
Key characteristics include:
- Understanding basic Six Sigma concepts
- Participation in project teams
- Contribution to data collection and analysis
The appeal of being a Yellow Belt lies in its accessibility. Many organizations encourage employees to become Yellow Belts because the training is less intensive compared to higher belts, making it a beneficial choice for those wanting to get their feet wet without committing to rigorous project management or statistical analyses.
One unique feature of the Yellow Belt is its broad applicability. While they may not make decisions, the awareness they gain can catalyze process improvements even in day-to-day operations. However, they may face challenges in influence and decision-making given their less central role.
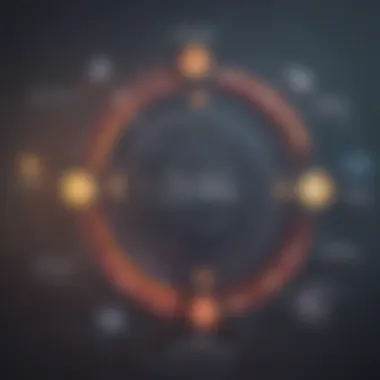

Green Belt
Green Belts have a deeper involvement than Yellow Belts. Often balancing their primary roles with Six Sigma responsibilities, they lead smaller projects and sometimes assist Black Belts. Their contribution is vital because they have enough understanding to apply Six Sigma concepts effectively and can drive change within their teams.
Key characteristics include:
- Leading small to medium-sized projects
- Using data analysis tools with greater effectiveness
- Encouraging team engagement in projects
The Green Belt is a popular choice for many as it strikes a balance between responsibility and manageable commitment. This level empowers professionals to take initiative regarding process changes, which is immensely valuable in organizations looking to foster a culture of continuous improvement. The downside may include time constraints as Green Belts juggle their primary roles with their Six Sigma projects.
Black Belt
Black Belts represent advanced competence in Six Sigma methods. They function as project leaders, managing cross-functional teams and ensuring that projects align with strategic business goals. Due to their expertise, they are often charged with training and mentoring Green and Yellow Belts as well.
Key characteristics include:
- Directing complex projects with significant improvements
- Training project team members
- Strong statistical and analytical skills
Having a Black Belt on a team can be a game changer. Their knowledge is indispensable for tackling tough problems and achieving substantial process improvements. This belt commands respect as Black Belts possess a profound understanding of Six Sigma methodologies. However, the role demands a significant time commitment and expertise that might come with a daunting learning curve.
Master Black Belt
Master Black Belts are the elite of Six Sigma practitioners. They not only lead major projects but also play vital roles in strategic planning and organizational improvements. They are usually responsible for developing Six Sigma training programs and fostering the overall Six Sigma culture within the organization.
Key characteristics include:
- Expert in Six Sigma methodologies
- Leading multiple project teams
- Oversight and guidance for other belts
This role is often seen as the pinnacle of Six Sigma involvement and is perfect for those passionate about quality improvement. Master Black Belts are invaluable as they're not just problem-solvers; they help shape the future of how the organization approaches quality. Despite the prestige, the expectations can be high, and the role may involve extensive pressure to deliver meaningful organizational results.
Project Teams
Project teams in Six Sigma play a fundamental role in ensuring that initiatives deliver improvements and enhancements. These teams are typically cross-functional, bringing together diverse perspectives and insights critical for identifying inefficiencies and implementing solutions. By integrating different areas of expertise, project teams can ensure that Six Sigma efforts reflect a holistic approach to process improvement.
In summary, the roles within Six Sigma—from Yellow Belt to Master Black Belt—are designed to foster accountability, drive change, and elevate a company's operational capabilities. These roles enhance Six Sigma's utility in real-world applications, enabling teams to tackle challenges effectively and achieve their objectives.
Tools and Techniques Used
When it comes to Six Sigma, the right tools and techniques can make or break a project. These methodologies not only streamline processes but also drive the quest for quality and efficiency. By understanding these tools, organizations can set a strong foundation for successful improvement initiatives.
Statistical Process Control
Statistical Process Control (SPC) is essential in the Six Sigma toolkit. It employs statistical methods to monitor and control processes. Imagine a coffee shop that measures the time taken to brew a cup. By tracking this process, they can identify trends and variations.
SPC helps in detecting problems before they escalate. For example, if the brewing time begins to exceed the usual limit, a coffee shop manager can investigate and resolve the issue instantly. This proactive approach reduces waste and maintains product consistency. Key benefits of SPC include:
- Early detection of issues: Spotting deviations in real-time allows for quick action.
- Data-driven decision-making: Leaders can make informed choices based on reliable data, reducing guesswork.
- Sustained performance: Continuous monitoring leads to consistent quality, which is crucial for customer satisfaction.
Process Mapping
Process mapping is another vital tool in the Six Sigma arsenal. It provides a visual representation of workflows, allowing teams to see every step involved in a process. Visual aids can make a world of difference, much like a well-drawn roadmap on a long journey.
These maps highlight inefficiencies and redundancies, guiding organizations in simplifying and standardizing their operations. For instance, in a healthcare setting, a process map might show how patients flow from check-in to exam rooms. By analyzing this map, organizations can identify bottlenecks and improve patient experience. The benefits of process mapping include:
- Clarity in operations: Everyone in the team understands the flow, reducing miscommunication.
- Improved collaboration: Clear mapping leads to better teamwork, as roles and responsibilities become apparent.
- Streamlined processes: Identifying unnecessary steps allows for the removal of waste, thus enhancing efficiency.
Root Cause Analysis
When problems arise, often the symptoms overshadow the real issue. This is where Root Cause Analysis (RCA) shines—it digs deep to uncover the underlying causes of problems. Think of it like using a shovel to unearth a buried treasure; only by finding the roots can true solutions emerge.
RCA tools, such as the Five Whys Technique and Fishbone Diagram, enable teams to explore issues systematically. For example, if a product fails quality checks, a team might employ the Five Whys. They would start with the question, "Why did this happen?" and keep asking until they reach the core of the problem. The major advantages of RCA are:
- Effective problem-solving: By targeting root causes, solutions become more impactful and enduring.
- Prevention of future issues: Addressing root causes reduces the risk of recurrence, leading to long-term improvements.
- Better team dynamics: Engaging in RCA fosters a culture of collaboration and open communication, essential for any successful Six Sigma initiative.
Overall, understanding and utilizing these tools and techniques can elevate a Six Sigma project from ordinary to extraordinary, making the difference between success and failure. As organizations strive for excellence, these methods enable them to implement effective solutions and achieve significant results.
Application of Six Sigma
The application of Six Sigma is crucial for organizations striving to minimize defects and consistently enhance operational excellence. Companies across various sectors have harnessed this methodology to refine their processes, boost their effectiveness, and, ultimately, drive profitability. The importance of applying Six Sigma rests in its structured approach to problem-solving, which can yield significant improvements in quality and productivity. It aligns well with the need for data-driven decision making, crucial in today’s competitive landscape.
Manufacturing Sector
In manufacturing, the application of Six Sigma stands as a cornerstone for ensuring product quality. The industry is often burdened with variances that can escalate defects, leading to waste and financial losses. By leveraging the Six Sigma principles, organizations can identify the root causes of variations. Tools like Statistical Process Control (SPC) are employed extensively to monitor processes.
For instance, consider a company producing automotive parts. They implemented Six Sigma to reduce defects in their production line. By analyzing metrics such as defect rates and cycle times, they discovered a pattern indicating that variations in temperature in the molding process were significant.
Key benefits of applying Six Sigma in manufacturing include:
- Reduction in Defects: Lowering the defect rate directly correlates with increased customer satisfaction.
- Cost Efficiency: Fewer defects lead to lesser rework and scrap costs.
- Enhanced Compliance: Meeting industry standards becomes more manageable, ensuring a brand’s credibility.
Service Sector
In the service sector, the application of Six Sigma is often less visible yet equally impactful. It allows service organizations to refine their processes, enhance the customer experience, and reduce operational inconsistencies. Take a banking institution, for example. They might deploy Six Sigma to analyze their account opening procedures. By segmenting each step of the customer journey, they identified bottlenecks that delayed service delivery, thereby frustrating customers.
Benefits of Six Sigma in this sector include:
- Increased Efficiency: Streamlined processes lead to faster service and reduced wait times.
- Improved Quality of Service: By focusing on customer feedback, organizations can adapt and tailor their services to meet expectations better.
- Data-Driven Insights: Organizations accumulate critical data that informs management decisions.


Healthcare Systems
The healthcare industry has also made strides in applying Six Sigma methodologies. In a realm where precision is paramount, the implications of errors can be severe. Hospitals that adopt Six Sigma practices focus on various aspects, from patient care to administrative tasks, ensuring an efficient flow of information.
For instance, a hospital might utilize Six Sigma to decrease patient wait times in the emergency room. The analysis reveals that the root of the delays often came from poor triage processes. Consequently, staff was trained to follow stricter guidelines, and as a result, the time from patient intake to treatment was significantly reduced.
By focusing on Six Sigma here, the benefits can include:
- Patient Safety: Enhancements in processes often lead to fewer errors in medication administration.
- Cost Reduction: Optimizing supply chain processes leads to financial savings.
- Higher Patient Satisfaction: Efficient care pathways improve the overall experience for patients.
Six Sigma's application across various sectors not only drives process improvements but also instills a culture of continuous growth and accountability.
Challenges in Implementing Six Sigma
Implementing Six Sigma isn't just a walk in the park; it often feels like climbing a mountain. Organizations face various hurdles when they set out to integrate Six Sigma into their operations. Understanding these challenges is crucial for anyone involved in this transformation. Recognizing what one might stumble over helps in strategizing and planning effectively. Here, we will delve into cultural resistance, resource allocation, and the sustainability of improvements, unearthing how these aspects can dictate the success or failure of Six Sigma initiatives.
Cultural Resistance
One of the most significant barriers to implementing Six Sigma is cultural resistance. Often, long-established companies develop a set of beliefs and practices that become ingrained in their daily operations. This culture can resist change, viewing new methodologies as threats rather than opportunities. Employees may feel that Six Sigma undermines their expertise or disrupts their workflow.
Communication plays a foundational role in overcoming this hurdle. Organizations need to demonstrate how Six Sigma complements existing processes, rather than conflicts with them. Workshops and seminars can help employees understand the benefits of a structured approach to improving quality. Changing the mindset is a slow process, but a consistent top-down approach where leadership advocates for Six Sigma can significantly ease this transition.
"Cultural change doesn’t happen overnight; it’s a journey, not a destination."
Resource Allocation
Resource allocation in Six Sigma implementation is like piecing together a complex puzzle. Companies often underestimate the manpower and time required to embed Six Sigma practices within their operations. Project teams need to be assembled, trained, and sustained, which can be a daunting task for organizations already stretched thin.
Moreover, lacking sufficient funding for training programs or project management tools could stymie progress. The task is to balance between investing adequately in resources and not overwhelming other areas of the business.
Effective planning is indispensable. Organizations should conduct a thorough analysis of their current resources and ascertain what additional support is necessary. This preparation can prevent unnecessary bottlenecks later on. Investing in quality training and project management tools can lead to substantial long-term benefits, turning Six Sigma implementations into success stories.
Sustainability of Improvements
Lastly, the sustainability of improvements poses yet another challenge faced by firms looking to implement Six Sigma. It’s common for organizations to see a spike in efficiency and quality upon the initial rollout of Six Sigma methodologies. However, without a plan to maintain these improvements, gains can turn out to be short-lived.
Sustaining improvements requires ongoing training, monitoring, and adherence to Six Sigma principles. Organizations must encourage a culture of continuous improvement where staff are aware that the pursuit of excellence doesn’t stop after the first successes. Regular reviews and progress assessments can help ensure that the new processes remain effective over time.
In summary, while the road to implementing Six Sigma is peppered with challenges, a keen understanding of cultural resistance, prudent resource allocation, and the quest for sustainability can empower organizations to forge a pathway toward lasting change. Successful companies recognize that overcoming these barriers is not merely about adopting a new methodology but truly integrating the principles of Six Sigma into the fabric of their operations.
Evaluating Six Sigma Success
In the realm of Six Sigma, measuring the effectiveness is crucial. This evaluation not only helps in identifying what worked well but also sheds light on areas needing improvement. The importance of assessing Six Sigma’s success hinges on a few core elements that ensure organizations reap the full benefits of their efforts. Without a formal evaluation, it’s akin to sailing a ship without a compass — you may be moving, but you’re unclear about the direction or progress.
To get the most out of Six Sigma, organizations must select relevant metrics that align with their objectives. Here, the emphasis is on quantifiable goals, which can inform strategy adjustments along the way. Evaluating Six Sigma success brings clarity to how the methodologies applied contribute to overall business aims, such as cost reduction, quality enhancement, and customer satisfaction.
Key Performance Indicators
Key Performance Indicators (KPIs) are the bread and butter of evaluating Six Sigma's impact. These specific metrics provide tangible evidence regarding the outcomes of the initiatives undertaken. Some essential KPIs include:
- Defect rates: Measuring the frequency of defects in processes helps to ascertain the improvements made over time.
- Cycle time: This indicator shows the duration needed to complete a process, allowing organizations to track efficiency gains.
- Customer satisfaction scores: Ultimately, the satisfaction levels of customers should reflect the quality improvements made within the organization.
- Cost savings: This metric consolidates the financial impacts of implemented changes.
By closely monitoring these KPIs, companies can quantify their progress and make well-informed decisions moving forward. They become the lighthouse guiding organizations through murky waters, illuminating whether Six Sigma strategies need recalibrating or a fresh approach altogether.
Return on Investment Metrics
When discussing Six Sigma success, assessing return on investment (ROI) metrics is indispensable. ROI gives a clear picture of how beneficial the implementation of Six Sigma has been for an organization. To understand this more thoroughly, some pivotal aspects include:
- Initial investment: Understanding the costs associated with training, resources, and time spent is critical to calculating true ROI.
- Savings generated: These can stem from efficiencies achieved and errors reduced, leading to lower operational costs.
- Increased revenue: Improvements in quality often lead to enhanced customer loyalty and retention, subsequently boosting sales.
Implementing these ROI metrics allows stakeholders to see the financial justification for the efforts put into Six Sigma. It turns subjective impressions into objective financial data, which can persuade those who may remain skeptical about the program’s effectiveness.
Evaluating Six Sigma success effectively aids in refining strategies, ensuring progressive change within organizations.
In summary, evaluating Six Sigma success creates a foundation upon which further improvements can be built. Framing the conversation around KPIs and ROI metrics creates clarity, allowing organizations to measure real results from their Six Sigma endeavors. The ongoing evaluation becomes a tool for longevity in quality improvement.
Future of Six Sigma
In a rapidly changing business landscape, the future of Six Sigma is looking promising. Companies are recognizing the need for methodologies that not only enhance operational efficiency but also adapt to changing customer needs and technological advancements. Six Sigma is evolving, embracing new trends and demands that align with contemporary business practices. To gauge the potential trajectory of Six Sigma, we must consider multiple aspects: its integration with Agile methodologies, the emerging trends in process improvement, and how these developments shape its relevance in various industries.
Integration with Agile Methodologies
The Agile methodology has gained traction in recent years, particularly among tech firms. Understanding how Six Sigma integrates with Agile processes presents a unique opportunity for organizations to combine the strengths of both approaches. Agile focuses on flexibility, rapid iteration, and customer collaboration, while Six Sigma emphasizes data-driven decision-making and quality control.
When these two methodologies converge, the outcome can be profoundly beneficial. For instance, incorporating Six Sigma’s analytical tools within the Agile framework allows teams to identify defects and measure performance effectively throughout the project lifecycle. This integration cultivates a culture of continuous improvement, ensuring that while teams move swiftly, they remain equipped to maintain high standards of quality.
Here are some specific benefits of this integration:
- Enhanced Responsiveness: Agile equips teams to respond quickly to changes, while Six Sigma ensures these changes are beneficial rather than detrimental.
- Quality by Design: By utilizing Six Sigma’s tools, teams can design processes in a way that anticipates and mitigates defects.
- Customer-Centric Focus: Agile encourages continuous feedback from clients, which can be supported by Six Sigma metrics to measure satisfaction effectively.
This melding of practices is not without its challenges. Companies must be wary of cultural resistance, as employees might find it difficult to reconcile the meticulous nature of Six Sigma with the fast-paced environment of Agile. Training and open discussions will be essential in making this transition smoother as organizations move towards a more dynamic work environment.
Emerging Trends in Process Improvement
As businesses continue to evolve, so do the methodologies that support them. The trends in process improvement are becoming more diverse and increasingly technology-driven. Six Sigma is at the forefront of these transformations, prepared to adapt and grow.
Some notable trends include:
- Data Analytics and Big Data: The role of data in decision-making is expanding. Implementing advanced analytics allows for deeper insights, enabling organizations to identify inefficiencies and improve processes with precision that was previously unachievable.
- Automation: Robotic process automation is being integrated into various industries, streamlining tasks that were once manual. Combining this with Six Sigma methodologies can lead to remarkable enhancements in performance and accuracy.
- Sustainability Practices: There’s a rising emphasis on sustainable business practices. Incorporating sustainability metrics into Six Sigma projects not only positions organizations as socially responsible but also enhances efficiency — often leading to cost savings.
- Holistic Approaches: Modern organizations are looking beyond individual processes. Six Sigma can facilitate an integrated view of entire operations, promoting a more cohesive approach to quality and performance across departments.
Ultimately, combining traditional Six Sigma techniques with emerging trends can foster innovative solutions tailored for contemporary challenges. Companies that embrace these changes will not only enhance their process efficiency but also create long-lasting impacts in their respective industries.
"To thrive in the future, organizations must adapt Six Sigma principles to foster agility and leverage technology. A thoughtful integration ensures long-term success in a competitive landscape."